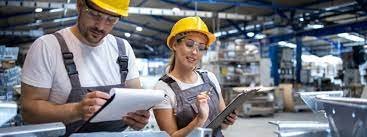
Quality Checks and Inspection
When it comes to turning a vision into reality, an interior design project is only as successful as the quality behind its execution. At Awesome Creators, we understand that aesthetics must meet functionality, durability, and precision. That's why our quality checks and inspections are deeply embedded into every stage of our design process—from initial concept to final handover. This commitment ensures that every space we craft is not just beautiful but also built to last.
Why Quality Checks Matter in Interior Design
In the interior design industry, the margin for error is minimal. A poorly installed light fixture, a mismatch in paint shades, or misaligned cabinetry can compromise the entire design aesthetic and client satisfaction. More importantly, these mistakes can lead to increased costs and extended project timelines. For Awesome Creators, quality checks are not an afterthought—they are a cornerstone of our service delivery.
Quality inspections help us:
-
Maintain high standards of craftsmanship
-
Ensure adherence to the approved design
-
Verify structural integrity and material quality
-
Avoid expensive rework and delays
-
Deliver lasting value to clients
Our Quality Assurance Philosophy
At Awesome Creators, quality isn’t just a checkbox—it’s a culture. We adopt a proactive, preventive approach to quality assurance. Our design and project management teams work collaboratively with our procurement, execution, and vendor partners to make sure that every component of the project adheres to our internal benchmarks and client expectations.
Our quality control measures are guided by three key principles:
-
Attention to Detail
-
Transparent Communication
-
Technical Precision
We believe that combining these principles ensures that no detail is overlooked, and no compromise is made on quality.
Quality Checkpoints Throughout the Project Lifecycle
1. Pre-Execution Phase
Design Approval & Mock-ups
Before a single nail is hammered, we carry out thorough quality checks on the design blueprints. This includes reviewing CAD drawings, 3D renders, and material selections. Mock-ups are created for key design elements like wall finishes, custom furniture, and lighting layouts. These are shared with clients for approval, ensuring their vision is fully captured before any on-site work begins.
Material Selection & Vendor Vetting
We work only with pre-qualified vendors and suppliers who meet our standards for quality, sustainability, and reliability. Every material—whether it’s wood, fabric, tile, or hardware—is tested for performance, durability, and aesthetic value before final selection.
2. Execution Phase
Site Readiness and Structural Checks
Before installations begin, our project managers inspect the site for structural soundness. This includes checking walls for moisture, floor levels, plumbing and electrical lines, and space measurements. Any discrepancies are rectified before moving forward.
Stage-wise Inspection Process
As work progresses, our quality control team conducts inspections at every critical milestone:
-
Carpentry Checks: Precision in joints, smoothness of finish, hinge alignment, edge banding, and structural strength.
-
Paint & Polish Inspections: Uniformity of texture, shade matching, and durability of paint or polish layers.
-
Electrical & Lighting Audits: Testing for load handling, proper grounding, correct fixture placement, and switch alignment.
-
Plumbing Checks: Ensuring correct gradient, leak-free joints, water pressure tests, and seamless fixture installations.
-
False Ceiling & HVAC: Checking for perfect levelling, concealed wiring, proper insulation, and air duct alignment.
We document each stage using photos, videos, and reports to maintain transparency with clients and to create a reliable paper trail of quality assurance.
3. Post-Execution Phase
Final Walkthrough & Snag List
Once the project is near completion, our team conducts a final inspection walkthrough. This involves preparing a detailed snag list—noting any imperfections, touch-ups, or missed installations.
Typical snag list items include:
-
Paint touch-ups
-
Door alignment issues
-
Loose handles or fittings
-
Minor chips or dents
-
Sealant applications
Each item is addressed before the final handover to the client.
Client Review & Handover
After resolving all snag list points, we invite the client for a walkthrough. During this session, we explain all installed systems (lighting, storage mechanisms, appliances), share care instructions, and hand over warranty documentation. Only after the client gives a formal sign-off do we consider the project complete.
Special Inspections: Safety & Sustainability
At Awesome Creators, we go beyond surface-level quality. We carry out special inspections to ensure compliance with:
-
Electrical Safety Standards (circuit protection, earthing)
-
Fire Safety (for commercial spaces: fire-resistant materials, clear exit paths)
-
Eco-Friendly Practices (low-VOC paints, sustainable wood, energy-efficient lighting)
Our clients value us not just for stunning interiors but for safe, sustainable environments that promote health and well-being.
Quality Control Tools & Technology
To stay ahead in the industry, we integrate modern tools into our quality inspection routines:
-
Digital Measurement Tools for accurate on-site verification
-
Laser Levels & Plumb Bobs for structural alignment
-
Project Management Software for real-time quality tracking and client updates
-
Thermal Cameras to detect moisture or electrical overloads in walls
-
3D Scanners to ensure as-built conditions match the design
These technologies allow us to improve precision, reduce human error, and deliver a higher standard of finish.
Training & Accountability
A system is only as good as the people who run it. That’s why we invest heavily in training our teams on new materials, construction techniques, and quality protocols. We also hold weekly reviews and daily checklists to monitor performance.
Every team—from carpenters and electricians to designers and site engineers—is held accountable to our strict quality benchmarks. And in the rare instance of an oversight, we take full responsibility and ensure prompt correction.
Final Thoughts: Built to Impress, Built to Last
Interior design is more than creating attractive spaces—it’s about creating environments that stand the test of time. With Awesome Creators, clients are assured not just of elegant designs, but also of robust execution and a hassle-free experience. Our comprehensive quality checks and inspections reflect our commitment to excellence, precision, and trust.
When you choose Awesome Creators, you choose peace of mind